Corporate Social Responsibility
As a responsible Danish workplace, we are inspired by the 10 principles of the UN Global Compact in the areas of human rights, labor rights, the environment and anti-corruption. We work with the 17 global goals and we have systematized our environmental work and in August 2020 we achieved a DS/EN ISO 14001:2015 certification.
Working conditions and working environment
For us, good working conditions and a good working environment are crucial factors in running a healthy business. Therefore, we attach great importance to ensuring good and safe physical and mental working conditions for our employees. We, of course, follow all applicable rules in this area and, among other things, prepare annual workplace assessments so we can constantly improve.
We show social responsibility in all employment matters and employ skilled labor, employees in flex jobs, and wage subsidies. Our staff is professionally organized and we have a much higher proportion of apprentices, always approx. 10% than required by law. We are a member of the Danish Industry and follow the Industry Agreement, which ensures that all employees have orderly conditions.
We always want to move forward and it is important with new inputs and ideas. That is why we often collaborate with students from Aalborg University and UCN on development projects in energy optimization, sales and marketing, production optimization, HR and management. In addition, we have completed a major health project for all employees focusing on diet, smoking, alcohol, exercise and stress.
Quality, environment, and ISO certifications
We produce products of the highest quality, with a long lifespan, and the longest service life of the industry. Our products are reliable and manufactured according to a number of ISO certifications.
We have a DS/EN ISO 9001:2015 quality management system, which ensures a uniform product quality and efficient work processes. In addition, we have a number of welding certifications such as DS/EN ISO 9606-2 for the construction of tanks according to EN 13094:2015 as required by ADR 2017, DS/EN ISO 10042:2005 for arc welding of joints in aluminum and its alloys and DS/EN ISO 13445-4: 2017 for the design and manufacture of pressure tanks. In addition, we are ISO certified according to the standard DS/EN ISO 3834-2:2005 to meet quality requirements for melt welding of metallic materials.
Besides our ISO certifications, we work with LEAN management to ensure that we constantly optimize our production processes.
In August 2020, we became DS/EN ISO 14001:2015 certified and we are the only tank builder in Northern Europe with both an ISO 9001:2015 and ISO 14001:2015 certification. In 2022, we achieved a DIN 2303-Q2BK1 certification. The certification in DIN 2303-Q2BK1 means that we are now approved to weld in all types of steel (except reinforced steel) according to German welding standards.
In December 2024, we became EN ISO 27001:2022 certified. It is a management system within cyber and information security, which is also close to the NIS2 directive from the EU. We have raised our security level considerably and will also continue to allocate resources to combat the ever-increasing cyber threats.
Environment and climate
We have already made a large number of improvements in the company, all of which contribute to making the company greener. We’re not quite finished, but we’re well underway. We have reduced our energy consumption considerably and completed a number of digitization projects, which also have a positive effect on the environment.
Ongoing projects
We continue to work with a wide range of initiatives that will further reduce our energy consumption and environmental impact. Currently we are working on:
- Replacing our heating system in the test hall from an oil boiler to district heating.
- Sealing of compressed air systems.
- Participation in the “Wild nature” project in connection with the new cycle path along Hadsundvej.
Digitization
We have completed a number of digitization projects that also help save energy consumption, and we are embarking on a major digitization journey. So far we have:
- Reduced paper consumption in our work processes.
- Increased productivity in our production using digital technical documentation.
- Reduced production delays by implementing electronic inventory scanning system with bar codes.
- Reduced unnecessary driving on urgent orders.
UN´s 17 Sustainable Development Goals
HMK Bilcon work with UN’s 17 Sustainable Development Goals. We are also part of the global community that takes responsibility for the globe, which is why we have decided to focus on the most relevant development goals for us where we can make improvements now.
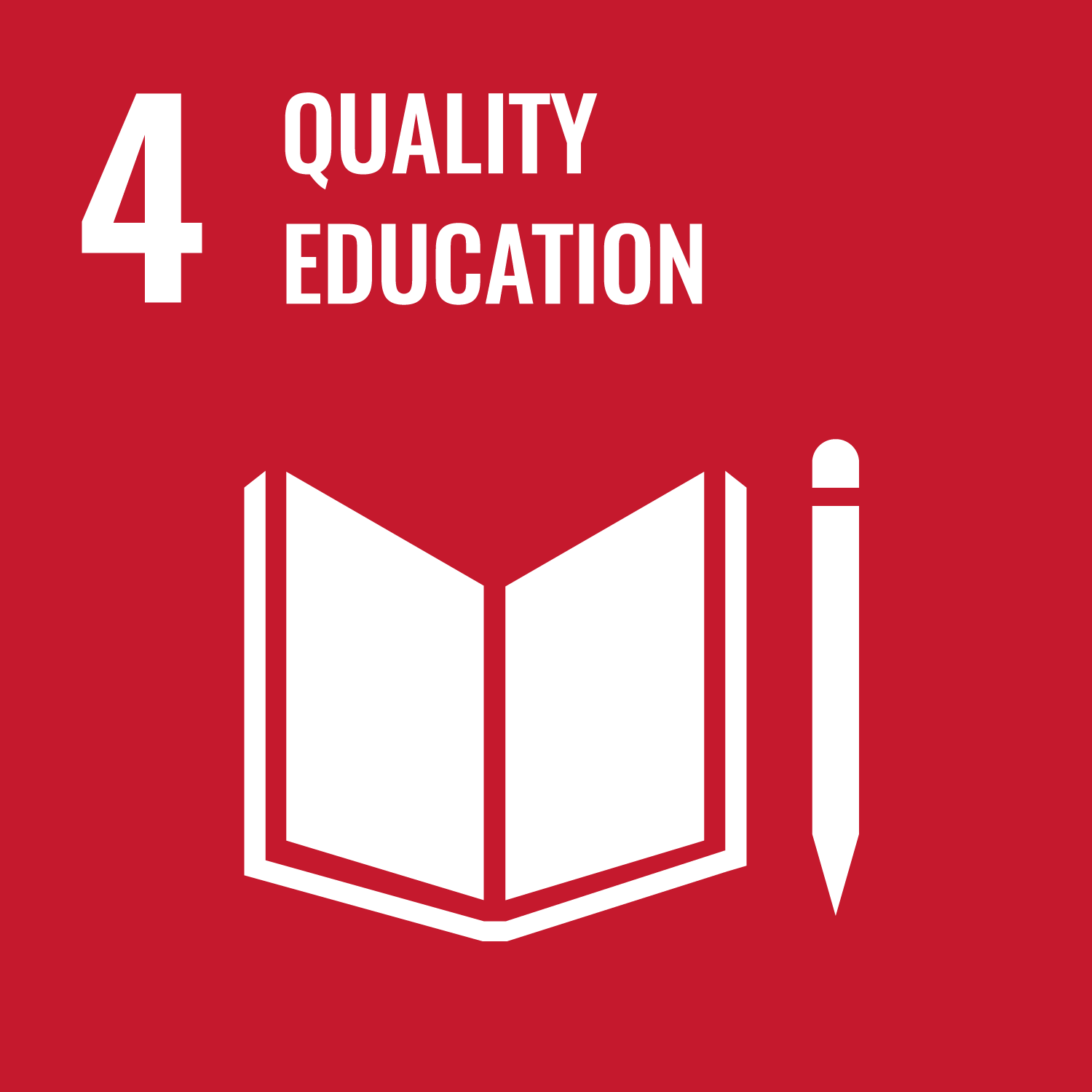
- We work closely together with educational institutions to help students and apprentices develop professional skills and competencies.
- We always have 10% apprentices employed.
- We have employees in flex jobs and wage subsidies.
- All employees are offered continuing education in i.a. LEAN.
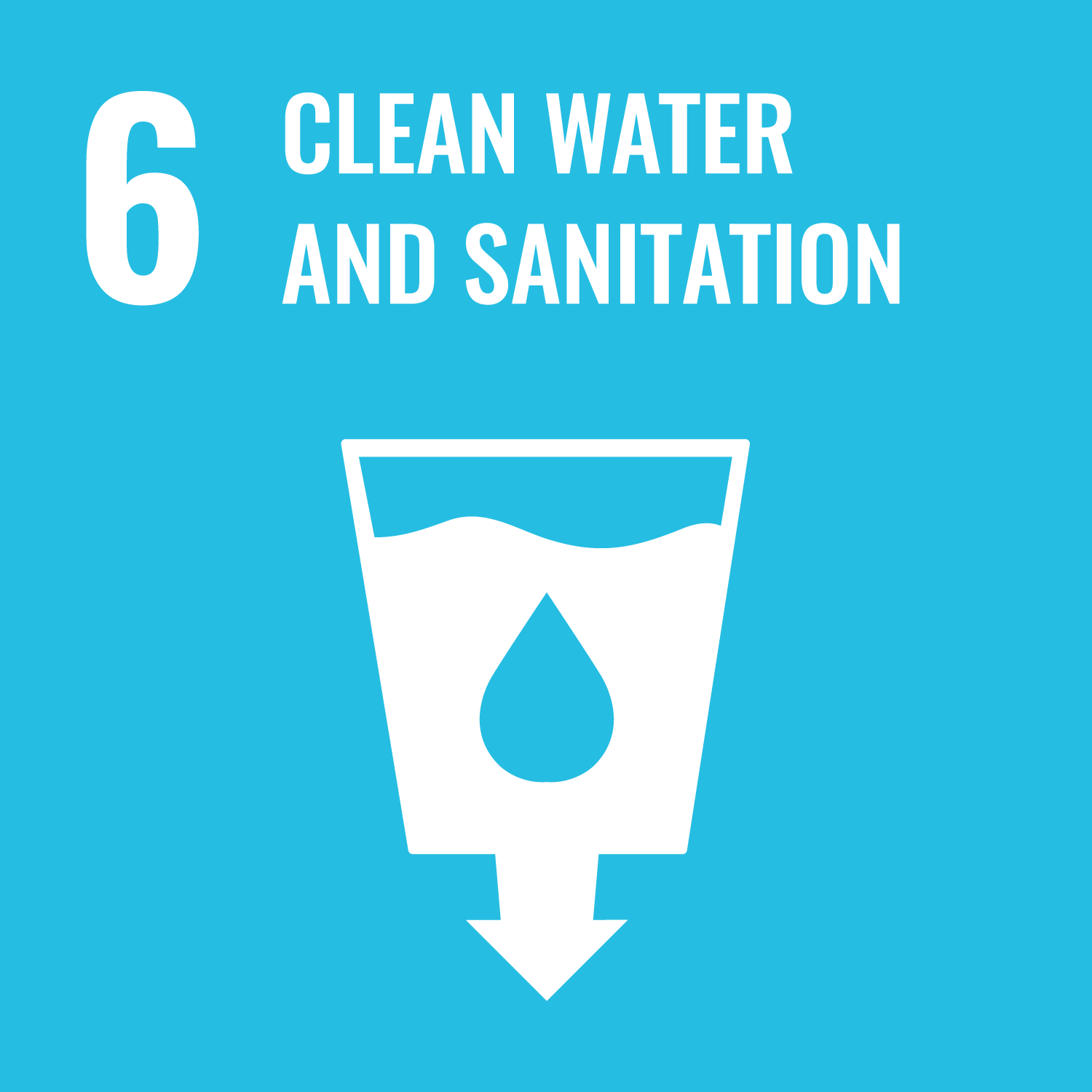
- We recycle water for pressure testing.
- We continuously reduce water consumption.
- Washing places are connected to wells with oil separators.
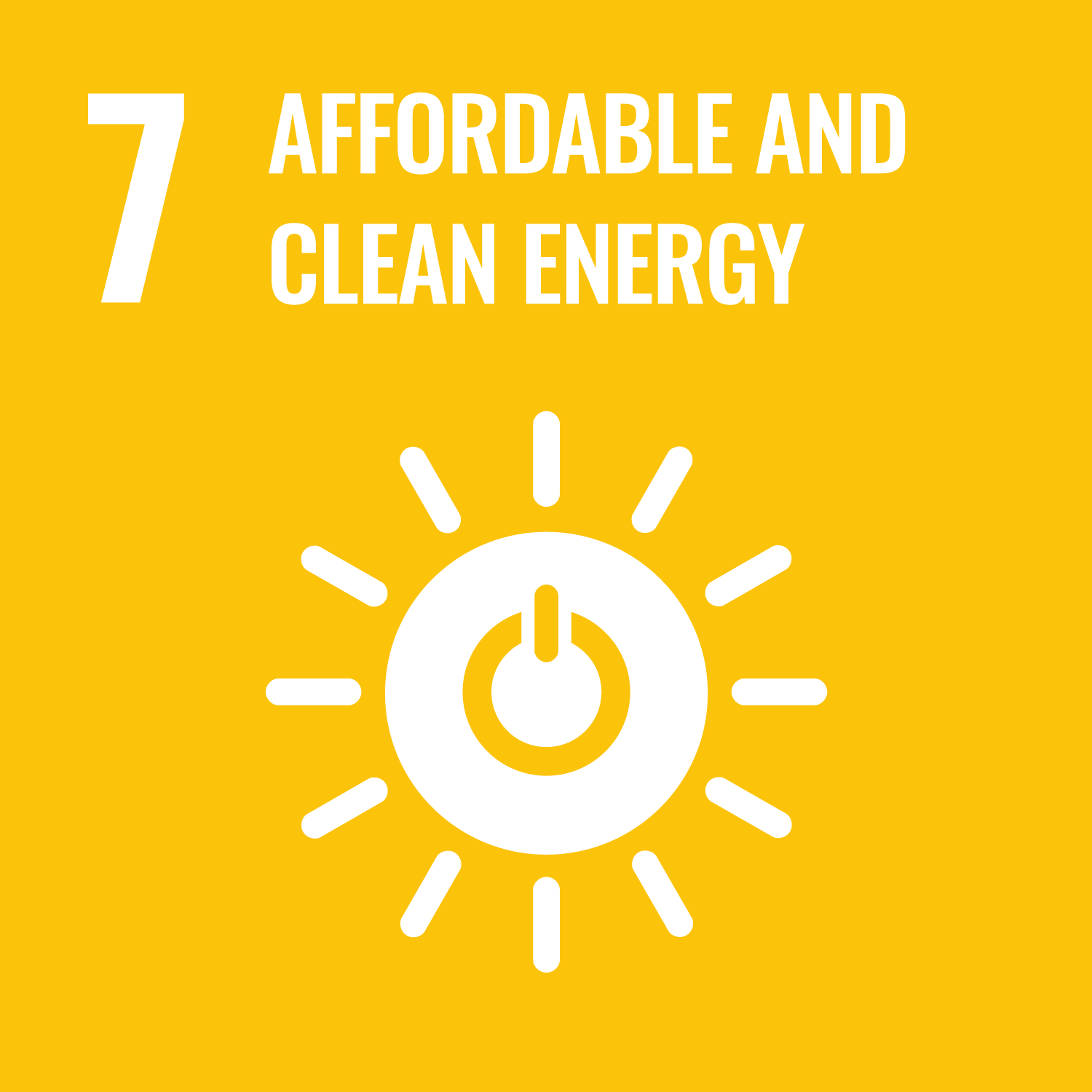
- We will continuously optimize energy throughout the company.
- We work on integrating solar cells into our products.
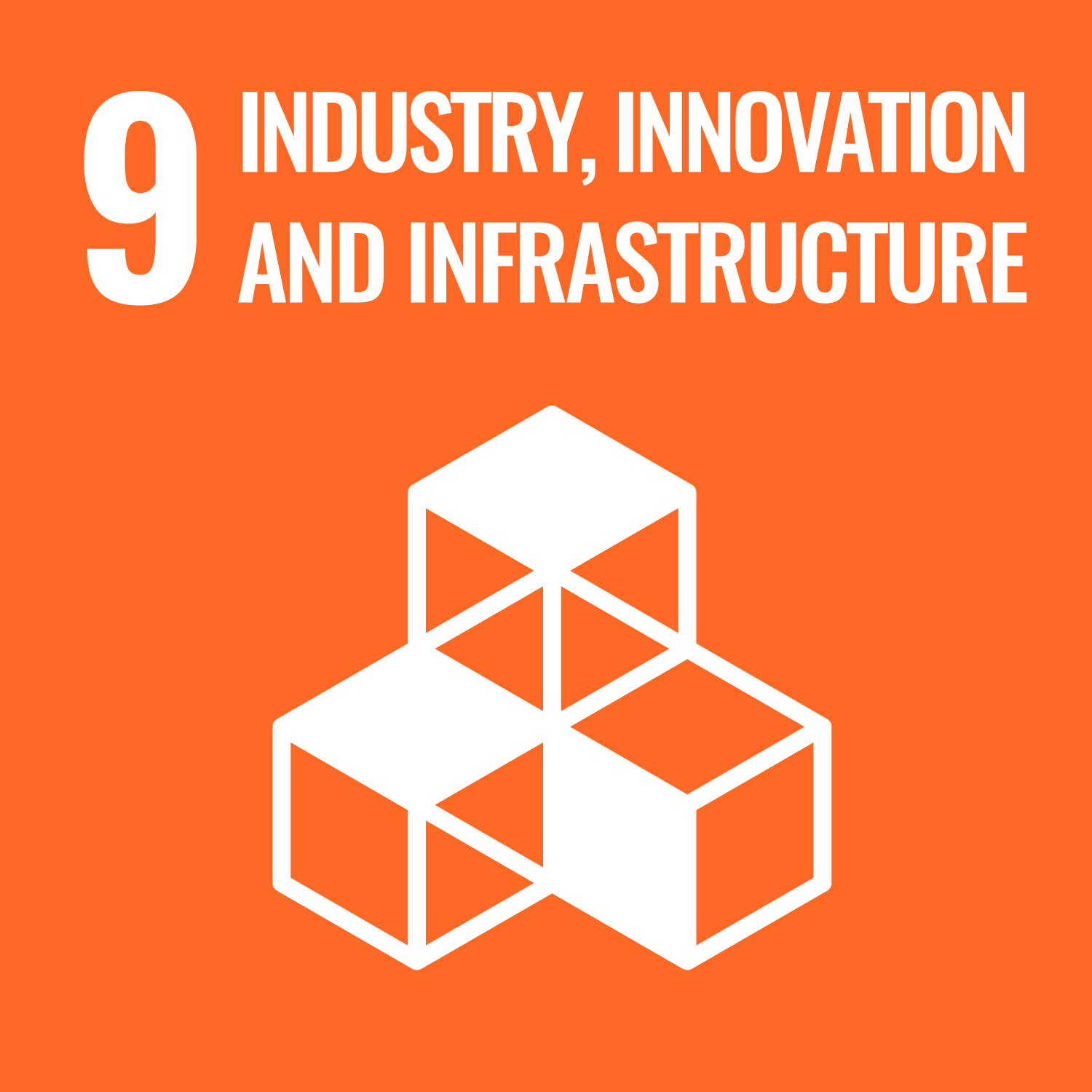
- We use LEAN management to increase production efficiency.
- We want to make more efficient use of resources and increase the use of clean and environmentally friendly technologies and industrial processes.
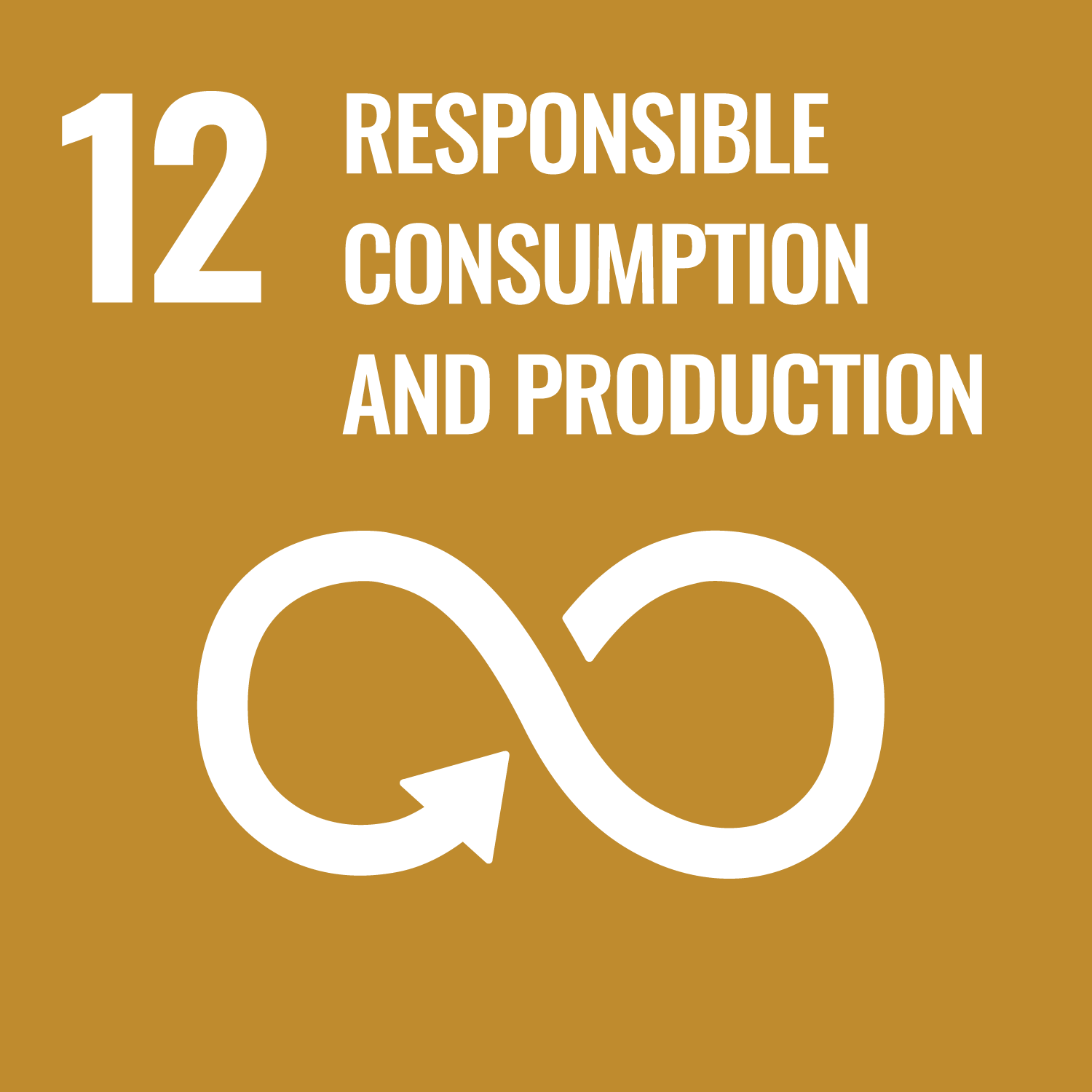
- We handle chemicals and waste environmentally safe.
- The amount of waste must be significantly reduced through prevention, reduction and recycling.
- Integration of sustainability information into our reporting cycle.
- 95% of our computers, servers and phones are bought refurbished.
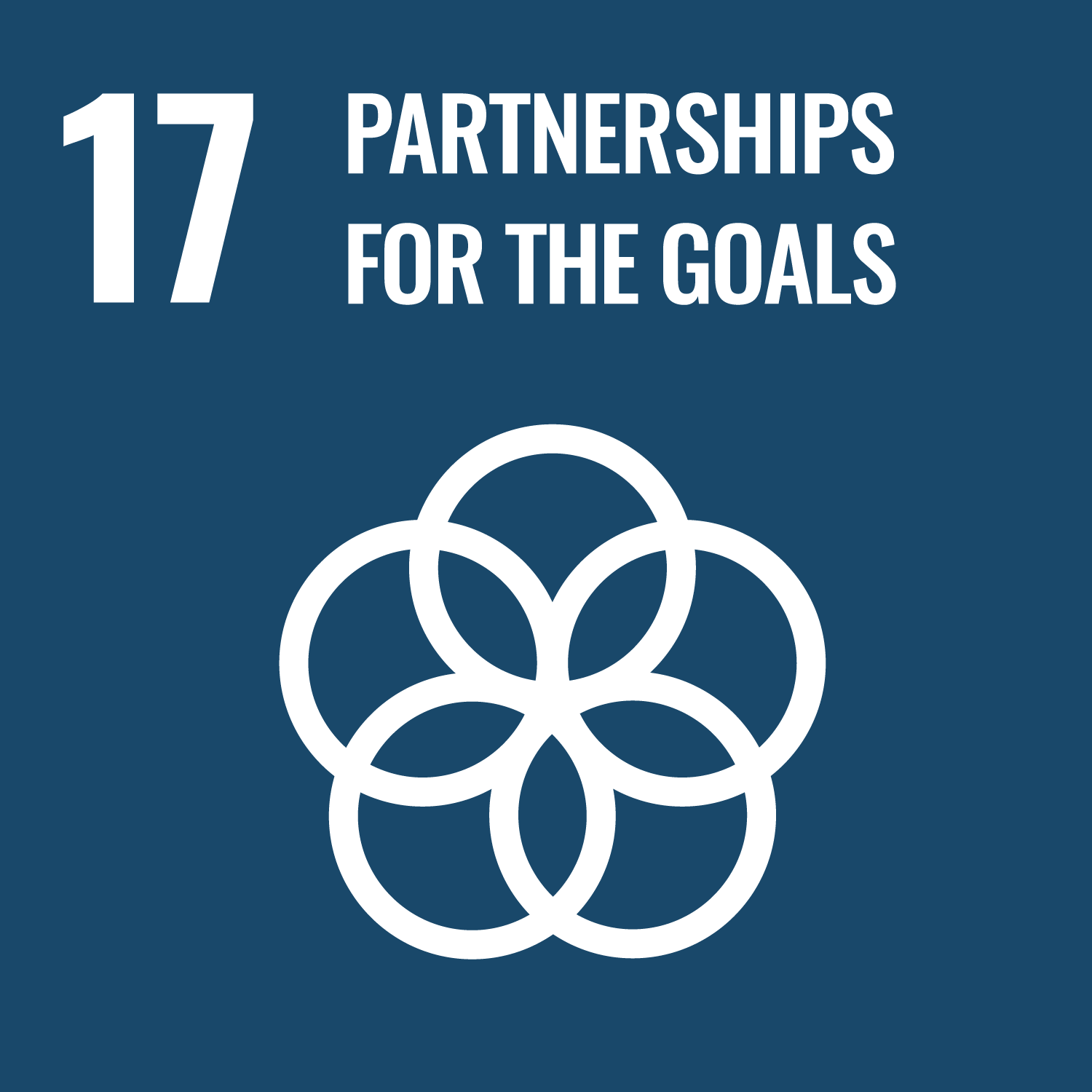
- We are an active member of the Network for Sustainable Business Development Nord Denmark and participate in sustainable development projects e.g. The Green Travel Team.
- We work closely with Business Aalborg on various development projects.
- We work with House of Energy to do green screening and green strategy.
- We are a member of the Aalborg Alliance and Klimaalliancen.
- We collaborate with High:five to help young people on the edge back into the labor market
Improvements made in 2018-2022
- 100% of our electricity came from renewable energy sources such as hydropower and wind energy in Denmark and Norway.
- We have invested one million in a new paint booth and an industrial gas plant (LPG), which has halved energy consumption for heating and reduced CO2 emissions by 13% and S2 by 97% and NOX by 65%.
- Lighting in production halls and office buildings is 100% LED and energy saving bulbs.
- New frequency controlled compressor has reduced electricity consumption by approx. 20-30%.
- The consumption of district heating has been reduced by approx. 20-30% via district heating control.
- All caloriferes have been cleansed and replaced with newer more efficient models.
- 8 smaller heat pumps have been installed to supplement heating.
- Electric water heaters have been installed instead of oil water heaters in the assembly hall.
- New faucets have been installed in bathrooms and toilets.
- Two new low pressure ventilation systems with heat recovery and frequency control have been installed.
- All local exhaust ventilations have been sealed.
- All gates have been sealed.
- Ceiling have been insulated over all paint booths.
- Reduced consumption of paint by 20% when switching to better products.
- Purchase of new welding appliances that use less power.
- Washing places are connected to wells with oil separators.
- We sort waste for recycling incl. steel, stainless steel, aluminum and flammable material.
- 90% of cardboard and cardboard boxes are recycled for shipments.
- We only use transporters that at least comply with the EU5 standard.
- All vehicles have been replaced with new models that run twice as far on the liter, which applies to both forklifts and company cars.
- New electrical forklifts, pallet trucks, sweepers, tractors and heavy duty truck with lower emmisions have been purchased.
- Floors painted bright to improve working environment.
- New noise-reducing walls built with Troldtekt acoustic panels.
- Water recycling in pressure testing.